Necessary Pipeline Welding Inspection Tips for Quality Assurance
In the realm of pipe building and construction, the honesty of welds holds extremely important relevance to make certain the safety and security and effectiveness of the entire system. From natural gas to refined oil items, pipelines form the lifeline of numerous sectors. Exactly how can one ensure the high quality of these welds that connect the pipe sections? The solution hinges on meticulous inspection strategies and adherence to strict quality control requirements. By understanding the essential pipe welding evaluation tips, specialists can avert possible dangers, reduce pricey repair services, and promote the integrity of these vital facilities.
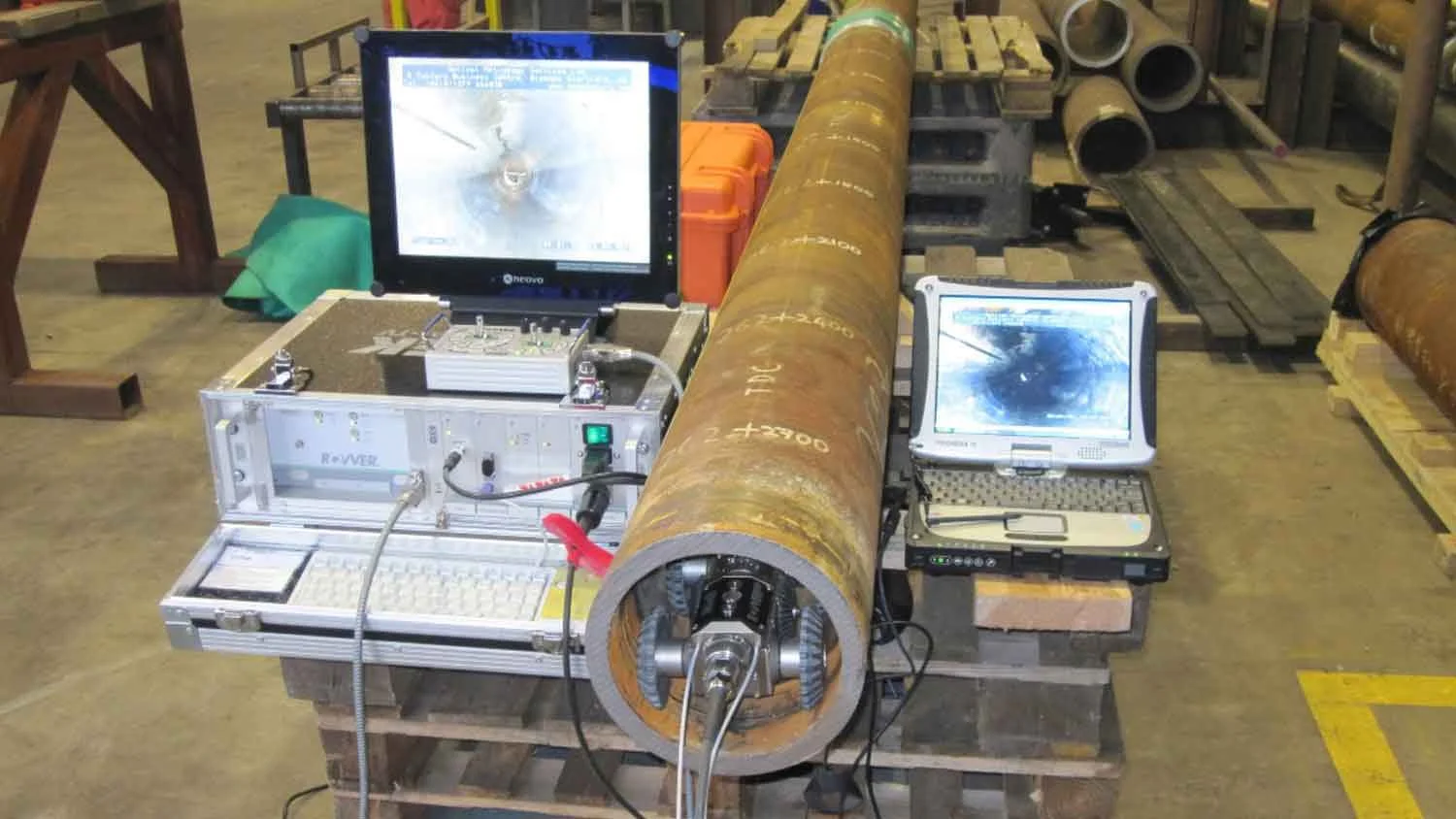
Significance of Welding Examination
Welding inspection plays a critical function in ensuring the structural honesty and safety of pipeline systems. By meticulously taking a look at welds, inspectors can recognize any defects or blemishes that could jeopardize the honesty of the pipeline. These assessments are vital for stopping leakages, ruptures, and various other possibly devastating failings that can result in environmental damages, economic losses, and even death.
The significance of welding assessment can not be overemphasized, as the quality of welds directly affects the total performance and longevity of the pipeline. Via non-destructive screening approaches such as visual evaluation, ultrasonic screening, radiography, and magnetic bit testing, assessors can discover problems that might not be visible to the naked eye. By determining and resolving these issues at an early stage, welding assessment aids to make certain that pipes meet industry standards and regulatory requirements.
Eventually, welding inspection is a crucial aspect of high quality assurance in pipeline building, maintenance, and repair work (Pipeline Welding Inspection). By upholding rigorous examination criteria, market professionals can reduce risks and promote the safety and security and dependability of pipeline systems
Common Welding Issues
Amongst the difficulties faced in pipe welding, typical issues can dramatically influence the structural integrity and efficiency of the welded joints. Some of one of the most common welding flaws consist of absence of fusion, porosity, fractures, insufficient penetration, and imbalance. Lack of blend happens when there is inadequate bonding in between the weld metal and the base steel, causing a weakened joint. Porosity, characterized by gas pockets within the weld, can lower the stamina and make the weld vulnerable to corrosion. Splits in the weld can circulate over time, jeopardizing the architectural stability of the pipe. Insufficient penetration takes place when the weld steel does not totally permeate the joint, causing a weak bond. Misalignment, where the weld bead is not correctly centered, can result in anxiety concentration points and possible failure. Detecting and addressing these common problems through comprehensive examination and high quality control processes are essential for guaranteeing the integrity and safety of pipeline welds.
Evaluation Methods for Pipelines
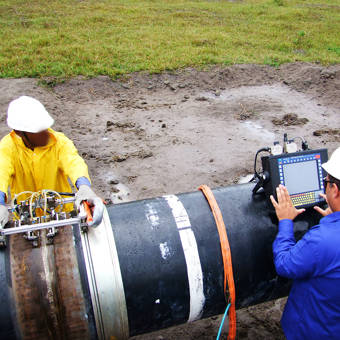

In making sure the architectural honesty and reliability of pipeline welds, the application of extensive assessment methods is extremely important. Numerous examination approaches are employed to detect potential problems and guarantee the general high quality of the welds. Non-destructive screening (NDT) methods such as radiographic testing, ultrasonic testing, magnetic particle testing, and liquid penetrant screening are generally made use of in pipe welding examination. Radiographic screening includes making use of X-rays or gamma rays to find inner issues, while ultrasonic screening utilizes high-frequency sound waves to identify imperfections. Magnetic particle screening is efficient for finding surface-breaking flaws, and liquid penetrant testing is used to spot surface cracks. Aesthetic examination is additionally necessary in pipeline welding to identify any kind of visible defects or gaps. Additionally, computerized examination strategies using advanced modern technologies like drones and robotics are progressively being employed to improve the efficiency and precision of pipeline evaluations. By using a mix of these examination strategies, pipeline bonded high quality can be assured, and prospective issues can be minimized before they rise into bigger next page problems.
Guaranteeing Quality Guarantee Specifications
To support rigorous top quality assurance criteria in pipeline building, precise adherence to developed market protocols and standards is crucial. Quality control in welding procedures requires a thorough method incorporating different phases of pipeline building and construction. Guaranteeing the top quality of welds includes making use of qualified welders, correct welding procedures, and adherence to sector standards such as those established by the American Oil Institute (API) and the American Society of Mechanical Designers (ASME) Inspection and screening play a vital function in confirming the honesty of welds, with methods like non-destructive testing (NDT) being vital for spotting possible defects. Furthermore, keeping detailed paperwork throughout the welding procedure is essential for traceability and quality Your Domain Name assurance objectives. Applying a robust high quality monitoring system that consists of regular audits and evaluations can additionally boost the overall quality control criteria in pipe welding. By focusing on adherence to these standards, stakeholders can guarantee the dependability and safety and security of pipe systems for the long-term.
Preventing Costly Fixings
Given the important relevance of maintaining strict high quality assurance requirements in pipe building and construction, an aggressive approach to preventing expensive repair services is necessary. Normal upkeep checks and surveillance of ecological factors that could impact the integrity of the pipeline are also crucial in avoiding costly repair work. By spending in preventative actions and focusing on top quality guarantee at every stage of the pipe welding process, business can reduce the risk of expensive repairs and ensure the long-term integrity of their framework.
Conclusion
In conclusion, adherence to proper welding inspection strategies is crucial for making certain the high quality and stability of pipelines. By recognizing usual welding flaws and executing comprehensive inspection procedures, expensive repairs can be stopped, and top quality guarantee standards can be met - Pipeline Welding Inspection. It is critical for pipeline welders to prioritize examination procedures to keep the security and reliability of the framework they are working with
The importance of welding examination can not be overstated, as the top quality of welds directly impacts the general performance and durability of the pipeline. Non-destructive screening (NDT) techniques such as radiographic screening, ultrasonic screening, magnetic bit screening, and liquid penetrant screening are typically made use of in pipeline welding examination. Visual examination is read this likewise essential in pipeline welding to recognize any noticeable defects or stoppages. Furthermore, computerized examination methods making use of advanced innovations like robotics and drones are progressively being used to enhance the effectiveness and precision of pipe evaluations.In final thought, adherence to correct welding inspection methods is crucial for guaranteeing the high quality and honesty of pipes.